
Abstract
This article investigates the environmental impact of PCB manufacturing, highlighting the importance of sustainable practices. We'll explore eco-friendly materials and production processes that minimize the environmental footprint. We'll also examine responsible waste management and recycling solutions that pave the way for a greener future in PCB production. Understanding the challenges and potential solutions provides valuable insights into building a more sustainable electronics industry.
Introduction
Printed Circuit Board (PCB) manufacturing is important for modern electronics. It does, however, present serious challenges to the environment. Many chemicals, such as solvents and etchants, are used in the production process, which might be dangerous if not handled carefully. Furthermore, the energy-intensive nature of PCB production adds to greenhouse gas emissions. Moreover, the production of PCBs produces a large amount of waste, including dangerous wastes and scrap materials.
Environmental Impact of PCB Manufacturing

Here's a breakdown of the key areas of the environmental impact of PCB:
Resource Depletion
PCBs are necessary for electronics, but making them poses environmental risks. There are major environmental effects associated with the extraction and processing of raw materials like metals (copper, aluminum), polymers, and chemicals (solvents, resins). Emissions from processing plants contribute to air pollution, which hurts human health, and chemical runoff from processing facilities can cause water pollution. Mining for metals like copper can disturb ecosystems, leading to land pollution. To mitigate these issues, regulations like the Restriction of Hazardous Substances (RoHS) directive restrict certain harmful materials in PCBs. Also, responsible manufacturers prioritize sustainable practices like recycling and waste reduction.

Waste Generation
The process of making PCBs produces a lot of waste. This waste includes leftover etching solutions, contaminated wastewater from cleaning and processing, and scrap metals (like copper) and laminates (like FR4) from fabrication operations. Improper waste management poses environmental risks, with heavy metals leaching into soil and water sources and untreated wastewater disrupting aquatic ecosystems. To mitigate these issues, regulations like the RoHS Directive restrict harmful materials in PCBs. Sustainable measures including recycling waste materials, employing less dangerous chemicals, and treating wastewater to reduce their environmental impact are also given top priority by ethical manufacturers. Through ethical procedures and managing waste generation, the PCB sector may lessen its environmental impact.
Hazardous Materials
Traditional materials used in PCBs can pose significant health and environmental risks. Although lead-based solders were originally preferred for their strong joints, it is now known that they are hazardous if swallowed or inhaled and can cause developmental problems and neurological damage, especially in children. The use of flame retardants, which are essential for preventing fires in PCBs, has sparked debate because of their associations with endocrine disruption, which may have an impact on hormonal balance and general health.
Regulations and advancements are driving changes to address these risks. As a result of the RoHS Directive's restrictions on potentially harmful materials like lead in electronic products, lead-free solder substitutes have become widely used and have reduced health concerns both during production and disposal. Research and development efforts aim to identify safer flame retardants that offer comparable fire protection without the associated health drawbacks.
Energy Consumption
Significant energy inputs are needed for several PCB manufacturing processes that are energy-intensive, like etching, drilling, and plating. These energy inputs frequently come from fossil fuels, which increases greenhouse gas emissions and has an impact on the climate. Recognizing the urgency for sustainability, the PCB industry is actively adopting greener practices. This entails putting energy-saving technologies into practice and streamlining procedures to cut down on energy consumption by upgrading equipment and changing workflows. Moreover, forward-thinking manufacturers are increasingly integrating renewable energy sources like solar and wind power into their operations to decrease reliance on fossil fuels, mitigate emissions, and promote a more sustainable production process overall.
Building a Sustainable Future: Solutions for a Greener PCB Industry
Fortunately, the electronics industry is increasingly embracing sustainable practices to minimize the environmental impact of PCB manufacturing. Here are some key strategies that are paving the way for a greener future:
1. Eco-Friendly Materials
Lead-Free Solder
The transition to lead-free solders from lead-based solders (SnPb) tackles serious health and environmental issues related to lead exposure. Typical choices for lead-free solder are:
SnCu: This 99.3% tin and 0.7% copper tin alloy has a higher melting point than SnPb, requiring soldering profile changes despite its strong solderability.
SnAgCu (SAC): SAC alloys, like SAC305 (3% silver, 0.5% copper), are widely used and, when matched to particular application needs, give good performance with lower melting points than SnCu.
Property | Lead Solder (Sn-Pb) | Lead-Free Solder |
Cost | Generally more affordable | Typically more expensive |
Electrical Conductivity | Slightly superior conductivity | Slightly reduced conductivity |
Reliability and Durability | More tolerant to stress and fatigue | Requires precise design and thorough testing |
Thermal Conductivity | 50 W/m·K | 73 W/m·K |
Melting Point | Lower melting temperature (183°C for Sn63/Pb37) | Higher melting temperature (217-227°C for common alloys) |
Wetting Properties | Superior wetting ability | Inferior wetting characteristics |
Mechanical Strength | More ductile and flexible | Less ductile, more prone to brittleness |
Tin Whisker Formation | Reduced risk of whisker growth | Increased risk of whiskers depending on the alloy |
Health Risks | Toxic; poses significant health risks | Safer alternative with no lead contamination |
Environmental Considerations | High toxicity due to lead presence | Lower toxicity; however, some materials may still pose risks |
Biodegradable Substrates
The traditional powerhouse of the PCB industry, FR4, presents an end-of-life challenge due to its non-biodegradable nature. However, bio-based polymers are emerging as a viable remedy for sustainable PCB substrates to address this problem. Although these materials offer significant environmental benefits, they also introduce new technical considerations, such as:
Material Types and Properties: There is a wide variety of bio-based polymers. Examples include the following:
Polylactic Acid (PLA): PLA has strong biodegradability and printability and is derived from renewable resources such as corn starch. But compared to FR4, it shows less heat resistance, which makes it less suitable for high-power applications.
Cellulose-Based Materials: These substrates use plant-based cellulose fibers, such as those found in wood. Although they have strong mechanical strength, they might have trouble matching FR4's electrical performance.
Bio-composite Materials: Researchers are exploring composites that combine bio-based polymers with reinforcing materials like natural fibers or recycled materials. These can offer a balance of biodegradability, strength, and electrical properties.
Technical Considerations: Integrating bio-based polymers into PCBs requires careful consideration of their unique properties:
Mechanical Properties: Biodegradable substrates may have varying degrees of strength and flexibility in comparison to FR4. This necessitates design modification to guarantee the PCB can withstand physical stress during operation.
Thermal Stability: As previously indicated, certain bio-based polymers are not as heat-resistant as FR4. This might restrict the effectiveness in high-power applications when a lot of heat is produced by the components.
Electrical Performance: Biodegradable PCB substrates offer an eco-friendly alternative to traditional FR4, but ensuring optimal electrical performance is challenging. Different dielectric constants can impact signal propagation speed and impedance matching. Also, varying coefficients of thermal expansion (CTE) can cause stress and potential delamination during temperature fluctuations.

Recyclable Metals
The fundamental components of conductive layers in printed circuit boards (PCBs) are copper and aluminum, whose innate recyclability encourages a sustainable electronics sector. Recycling these metals promotes a circular economy by reducing the exploitation of resources and the production of waste. It is possible to successfully reprocess and reuse recovered copper and aluminum from end-of-life PCBs in the production of new PCBs. Closed-loop recycling, where recycled metals contribute directly to new PCBs, reduces the need for virgin materials and minimizes environmental impact. Established recycling processes for copper involve crushing, milling, and separation, while aluminum recycling involves shredding, separation, and remelting.
2. Energy Efficiency

PCBs are the foundation of contemporary electronics, yet producing them can use a lot of energy. Nonetheless, the sector is adopting creative approaches to reduce its environmental impact. Process optimization is key, with manufacturers streamlining steps and investing in energy-efficient equipment like optimized lighting and temperature control units. Material efficiency is provided via additive manufacturing (3D printing), reducing waste and targeting energy use for specific areas. To lessen their dependency on fossil fuels, progressive manufacturers are also incorporating sustainable energy sources like solar and wind power. Adopting sustainability standards like ISO 50001 and Energy Star helps the sector transition to a more sustainable future by encouraging energy-efficient activities.
3. Proper Waste Management
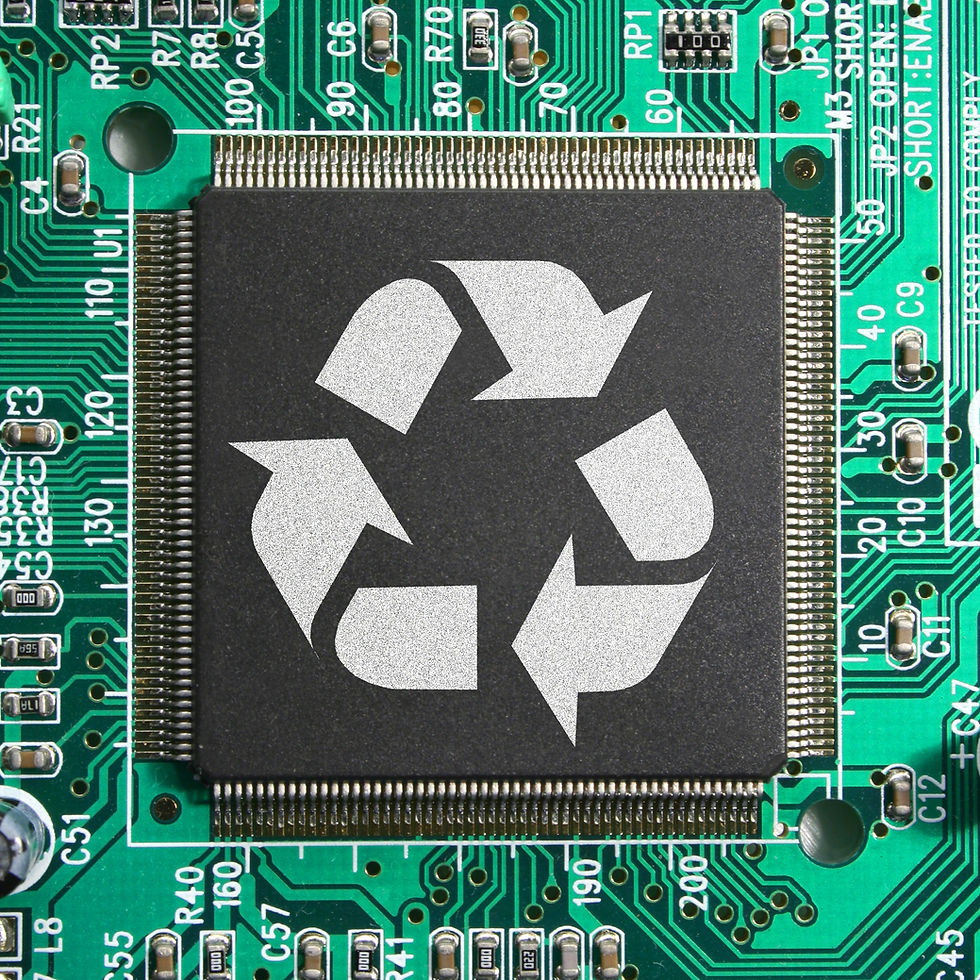
Recycling and Reuse: Metal recycling has two advantages. It provides a more affordable option for PCB manufacturers and lessens the environmental impact of extracting and processing fresh resources. Global guidelines such as the Responsible Minerals Initiative (RMI) encourage ethical procurement and conscientious recycling procedures all along the supply chain.
Hazardous Waste Treatment: Hazardous waste products from PCB fabrication might damage the environment if they are not disposed of properly. Responsible manufacturers identify and treat these threats: etching solutions like ferric chloride or cupric sulfate and cleaning agents are pinpointed as hazardous due to their potential environmental impact. These materials undergo neutralization reactions and precipitation techniques to render them less harmful before disposal. As a last option, treated waste may be incinerated with strict controls or landfilled per regulations like the Basel Convention, ensuring responsible treatment and disposal.
How to Achieve a Sustainable Future
Building a sustainable future for PCB manufacturing requires a collaborative effort. Manufacturers, designers, and consumers all have a role to play.

Manufacturers
Manufacturers can reduce the environmental impact of PCB manufacturing by using recycled or biodegradable materials instead of conventional FR4 substrates. For example, businesses such as IBM are exploring the application of bio-based materials, which lessens reliance on limited resources and reduces environmental impact over an extended period. It is essential to implement energy-efficient operations. Manufacturers may improve production processes and significantly reduce energy consumption by using cutting-edge technology like IoT for real-time monitoring and control. For instance, using LED lighting and variable-speed drives can save up to 30% on power use. Furthermore, ethical waste management minimizes contamination from mining and conserves raw resources. One example is Apple's closed-loop recycling of materials from old PCBs.
Designers
Designers can optimize PCB designs to minimize material usage, which involves techniques like high-density interconnects (HDI) that enable more components to fit on a smaller board, reducing the overall material footprint. Material recovery and component separation are made simpler by implementing design-for-disassembly concepts, such as the use of modular connectors and screws in place of adhesives. To ensure effective recycling and minimize electronic waste, modular connectors, for instance, make it easier to remove valuable metals like copper and gold from PCBs at the end of their lives.
Consumers
Consumers play a crucial role in promoting sustainable electronics practices by prioritizing products from companies committed to environmental stewardship. The PCB manufacturer has taken the lead in making sure that its products are energy-efficient and in employing renewable energy for its operations. Apple is another company like that. Their dedication also includes ethical recycling initiatives that allow users to recycle their old electronics, recovering and reusing precious elements like PCB metals. Customers can directly assist initiatives to decrease electronic waste and encourage a circular economy by purchasing products from firms that prioritize sustainability.
Please find more information for Electronic Donation and Recycling at: https://www.epa.gov/recycle/electronics-donation-and-recycling
Key Takeaway
PCB manufacturing presents significant environmental challenges due to resource consumption, energy use, and waste generation. Sustainable practices, including using eco-friendly materials, energy efficiency, responsible waste management, and collaborative efforts, are essential for mitigating these impacts and promoting a greener future. Recycling and the responsible disposal of hazardous materials are crucial steps in minimizing the environmental footprint of PCB production. Innovations in materials, manufacturing processes, and closed-loop systems offer promising avenues for further reducing environmental impacts.
TapRen, a PCB innovation and production leader, is at the forefront of these sustainable practices. By integrating advanced recycling techniques, eco-friendly materials, and energy-efficient manufacturing processes, TapRen ensures that its PCB production is both high-quality and environmentally responsible. Partner with TapRen for cutting-edge PCB solutions that prioritize sustainability and performance.
Comments